Advanced Techniques in Metal Stamping for Precision Production
As industries constantly require finer resistances and elaborate layouts in their steel elements, the pursuit for innovative strategies in metal stamping has increased. From the utilization of sophisticated multi-stage marking processes to the assimilation of cutting-edge automation technologies, the landscape of metal marking is going through a profound makeover.
Advanced Multi-Stage Stamping Procedures
Reviewing the complexities of sophisticated multi-stage stamping procedures reveals the advanced techniques utilized in modern production practices. Metal Stamping. Multi-stage marking is a complex process that involves several actions to transform a level sheet of steel into a last stamped product. Using progressive dies, where different procedures are carried out at each phase of the stamping procedure, enables high accuracy and efficiency in the manufacturing of complex steel components
During the preliminary phases of multi-stage marking, the level steel sheet is fed into the stamping press, where a collection of dies are made use of to reduce and form the material. Succeeding stages involve additional creating, bending, and punching operations to further refine the part. Each phase is thoroughly developed to develop upon the previous one, causing the development of complex geometries with limited resistances.
Advanced multi-stage marking processes require a high level of knowledge and accuracy to ensure the quality and uniformity of the stamped parts. By utilizing sophisticated equipment and tooling, manufacturers can create a vast array of steel components with effectiveness and accuracy.
Accuracy Tooling Innovations
Precision tooling developments have actually transformed the metal stamping sector, improving effectiveness and quality in producing procedures. These developments have actually dramatically influenced the means steel parts are generated, leading to greater accuracy and uniformity in the last products. One essential innovation is the development of computer system mathematical control (CNC) modern technology in tooling layout and construction. CNC systems permit detailed designs to be translated directly into tooling, making certain precision and repeatability in the marking process.
Moreover, the assimilation of sensors and real-time tracking capabilities in accuracy tooling has made it possible for manufacturers to spot and deal with issues quickly, lessening downtime and lowering scrap rates. By incorporating clever modern technology into tooling, drivers can optimize specifications such as stress, speed, and alignment throughout the marking operation, resulting in boosted item quality and boosted efficiency.
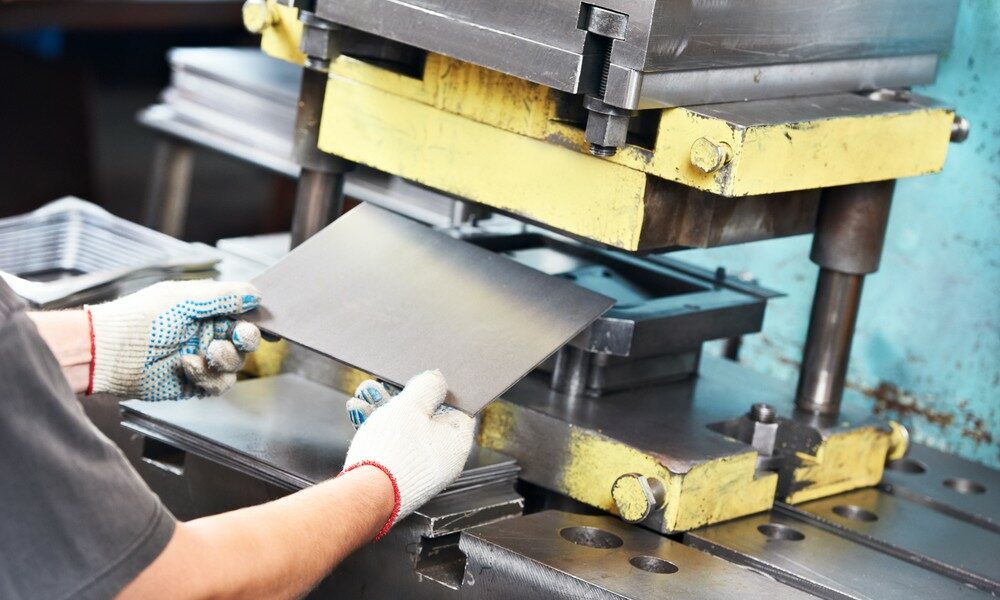
Automation in Metal Stamping
The development of accuracy tooling developments in the metal marking market has led the means for substantial advancements in automation, transforming the manufacturing landscape towards raised effectiveness and productivity. Metal Stamping. Automation in steel marking includes making use of sophisticated equipment and robotics to do different jobs traditionally executed by human operators. This change towards automation provides various benefits, consisting of improved precision, much faster production cycles, and minimized labor expenses
One secret facet of automation in metal stamping is the execution of computer mathematical control (CNC) systems, which enable exact control over the stamping process. CNC innovation permits for the creation of complicated and complex steel get rid of regular quality. Additionally, automated systems can be configured to run continually, resulting in greater outcome prices and shorter preparations.
Moreover, automation improves workplace safety and security by minimizing hand-operated handling of hefty materials and reducing the danger of crashes (Metal Stamping). As manufacturing markets click now remain to embrace automation, the future of metal marking holds terrific assurance for also greater performance and innovation
High-Speed Stamping Methods
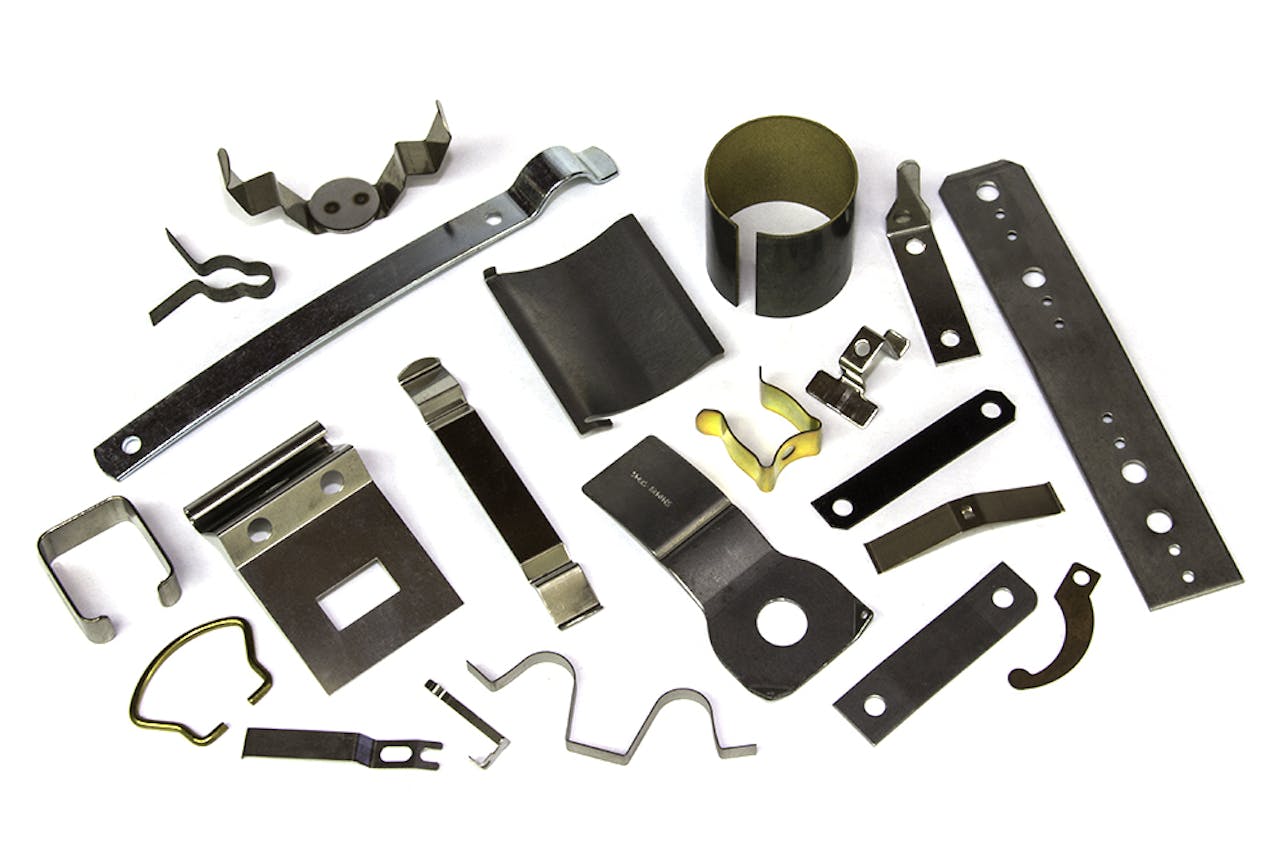
One of the primary benefits of high-speed stamping strategies is the capacity to produce a huge quantity of components in a shorter quantity of time compared to standard stamping methods. This enhanced efficiency not just permits manufacturers to meet limited production due dates but likewise enables cost financial savings through economies of scale. Furthermore, high-speed marking can help check out here in reducing product waste by maximizing the product usage throughout the marking procedure.
Moreover, high-speed stamping methods frequently incorporate cutting-edge features such as quick die change systems and real-time monitoring capabilities, additionally boosting the overall performance and adaptability of the steel stamping process. As technology remains to breakthrough, high-speed marking is expected to play a crucial duty in driving the future of accuracy production.
Quality Assurance in Stamping Procedures
Reliable quality control procedures are important for making sure the integrity and consistency of steel marking procedures. Quality control in marking procedures involves a collection of systematic processes targeted at identifying and protecting against issues in the manufactured elements. One crucial facet of quality assurance in steel stamping is making use of advanced examination methods such as optical assessment systems and coordinate gauging machines (CMMs) to validate the dimensions and tolerances of stamped parts.
Additionally, quality control procedures in marking procedures often consist of the execution of analytical process control (copyright) approaches to keep an eye on the production procedure in real-time and ensure that it remains within additional resources acceptable limits. By evaluating data and identifying patterns, manufacturers can proactively address any inconsistencies from the preferred quality standards.
Moreover, high quality control in metal stamping procedures likewise includes thorough product screening to ensure that the raw materials utilized satisfy the needed specifications for the stamping process. This might consist of performing product hardness tests, tensile toughness examinations, and dimensional inspections to ensure the high quality and stability of the stamped components. On the whole, implementing durable quality assurance procedures is essential for attaining top notch stamped components regularly.
Conclusion
In final thought, advanced methods in steel marking play an important function in accuracy manufacturing procedures. Via multi-stage marking procedures, innovative tooling services, automation, high-speed methods, and rigorous quality control actions, suppliers can accomplish greater levels of accuracy and effectiveness in their operations. These innovations in steel stamping technology have enabled firms to generate complex components with limited tolerances, inevitably resulting in boosted product high quality and client contentment in the manufacturing industry.